What is the Calibration of Measuring Instruments?
- October 05, 2023
- Registrationwala
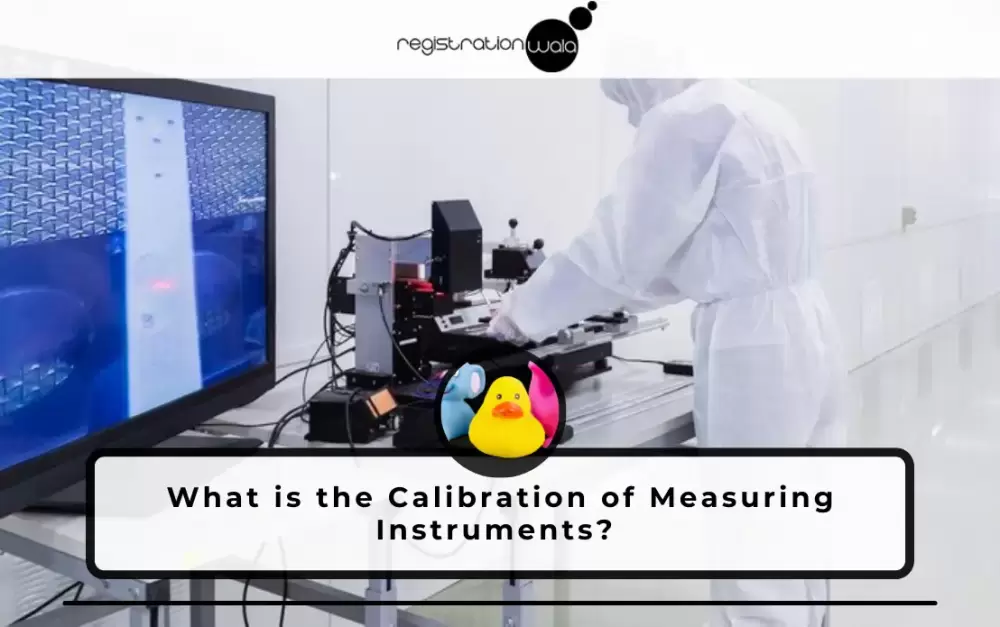
- Home
- /
- Knowledge Base
- /
- Regulatory License
- /
- Legal Metrology Certificate
- /
- What is the Calibration of Measuring Instruments?
What is the Calibration of Measuring Instruments?
The accuracy of all measuring instruments or devices degraded over time. This can happen because of hazardous manufacturing environments such as using different oils, metal chips, etc. The environment in which the instrument is being used has an effect on the measuring machine, if the environment is not proper the instrument will degrade quickly.
So, to maintain the quality of products and avoid any risk, frequent calibration is most important. The malfunctioning in the instrument can disrupt the measurement process or even pose a safety hazard. Below we shared why calibration of measuring instruments is important and when you focus on it.
What is Calibration Mean?
The calibration is a process to check that measuring instruments are working in accordance with their design, function and specifications. As per the Legal Metrology Department which provides legal metrology certificate “all the operations which are necessary for the purpose of determining the value of errors of weight or measures. If necessary Verification and stamping of the capacity of the Vehicle Tank or its compartment or any equipment is called Calibration of measuring instruments to determine the other Metrological properties of such weight or measures. Also includes the actual fixing of the position of gauge marks or scale marks may also be carried out with a view to permitting the use of weight or measures as a standard.”
The measuring devices should be calibrated as per the following points:
- As per the recommendations of the manufacturer.
- After any mechanical or electrical shock.
- Check on equal time intervals - monthly, quarterly, and annually.
Remember, the cost of un-calibrated measuring devices is much higher than the cost of calibration. So, it is recommended that measuring devices must be calibrated at some time intervals by professionals to ensure that all the errors will be corrected.
Benefits of Measuring Instrument Calibration
The following are the benefits of measuring instruments calibration:
1. Meet Standards: In the process of calibrating a measuring instrument, you must check that the device meets national and international standards. As it is important to ensure accuracy and consistency in production.
2. Reduce the Risk of Production Failure: Through the calibration, you can reduce the level of risk in production. The tools without calibration can lead to wrong measurement process and inaccurate results. Which can lead to production failure and defects. So, must do regular calibration to reduce the risk of such failures.
3. Improve Accuracy: Calibration helps in checking that measuring instruments provide precise and accurate results, resulting in superior-quality products.
4. Saving Costs with Periodic Calibration: The periodic calibration of measuring instruments will save the cost in audit fees by checking that all measuring equipment is up to standard. If calibration is not done, deviations in the measuring tool can result in inaccurate results and lower product quality which can lead to significant losses for the company.
Situations When Calibration is Required
All measuring tools operate differently and they require different working environments. Some devices can work in cold environments, whereas some require a warm environment. So with the change, it is important to calibrate measuring instruments to maintain the right function and temperature of the tool. Before starting a calibration process, it is better to check these things in the tool:
The new equipment calibration also be checked to ensure its working condition. This equipment should not be left as it is new, make sure that all its functions are working properly.
The calibration should be done on the equipment of the medical laboratory even if they finished the installation. The goal is to ensure the installation process is done correctly or not.
Periodic calibration is done to ensure that it is functioning properly and producing accurate results. The frequency of calibration will be determined by the consultant and create an appropriate schedule.
In case of damage or repair, the tool must be calibrated immediately to ensure proper function. The calibration must repeat as soon as the calibration period expires. It is done to make the instruments as per the international standards.
If a tool is producing irregular results, then immediate calibration is necessary. And, if a tool is not damaged, but there are doubts about the accuracy of results, a new calibration process should be carried out.
Why Calibration is Important?
In the calibration, the accuracy and quality of measurements are recorded with a piece of equipment. With time, the tendency for results and accuracy changes especially when using technologies or measuring parameters such as temperature and humidity. The goal of calibration is to minimise risk and uncertainty in the measuring instrument.
Calibration in the Food Industry
In catering or commercial kitchens, using a measuring instrument which is not calibrated can result in:
- Food safety issue
- Breach of HACCP and the customer becomes ill
- Notice from Environmental Health Officer for closure
- Legal action
All these things can damage the reputation of a business. As compared to the cost of your reputation, the cost of the calibration process is much less. So, it is not worth to ignore the calibration.
Calibration in Manufacturing
The equipment used in the manufacturing process must be calibrated at different points. It should done to check the reliable information for critical alarms and systems. In case of failure in calibration and improper calibration, it can cause injury, and death of employees and even cause major environmental issues.
Final Takeaway
To conclude, measurement is important and equipment calibration is most important. It builds confidence in the users and businesses in the result that they monitor, record and control. So, the process of calibration should not ignored and the type of this will depend on the type of instrument. Basically, the instruments that are performing critical operations must be calibrated frequently. However, the calibration can reduce the cost, ensure safety and increase the life and performance of instruments.
People also read: The Role of Dealers in India's Weights and Measures Industry
- 2405 views